다방면으로 방법 모색 중인 완성차 업체들
[미디어펜=김태우기자]친환경 바람과 더불어 자동차에 대한 소비자들의 인식과 기대수준이 높아지며 연비는 자동차 업계가 풀어야 할 최대 과제로 지목되고 있다.
이를 위해 많은 완성차 업체들은 제각기 다양한 방법을 통해 연비향상을 위한 연구개발에 투자를 아끼지 않고 있다.
|
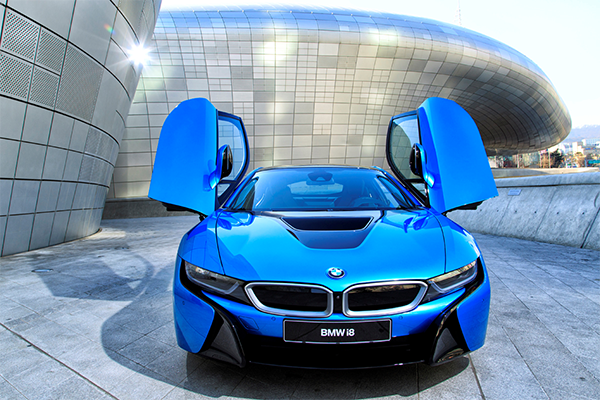 |
|
▲ 라이프 모듈은 신소재인 탄소섬유강화플라스틱(CFRP)으로 제작됐으며 드라이브 모듈은 알루미늄이 사용된 BMW i8/BMW코리아 |
16일 관련업계에 따르면 많은 완성차 업체들이 높아져만 가는 소비자들의 기대수준에 맞춘 연비향상을 위해 소재의 변화를 통한 원천적 무게 감량과 엔진 다운사이징 등을 위해 수많은 투자를 하고 있다.
특히 자동차의 경량화는 연비향상에 직접적인 연관을 되는 부분으로 각각의 업체들은 이를 위한 다양한 방법을 모색하고 있다.
이중 최근 많은 업체들이 선택하고 있는 것은 기본 구조를 이루고 있는 소재의 경량화다. 기본 골격을 이루고 있는 부분에 기존 금속보다 가벼운 소재를 사용하면 그만큼의 무게가 줄어들기 때문에 차체경량화에 유리하다. 다수의 제조사들이 알루미늄소재를 선호는 것도 이 때문이다.
최근 알루미늄보다 더 가볍고 튼튼한 소재들도 등장하고 있다. 그중 대표적인 것이 마그네슘을 활용한 신소재다. 마그네슘은 기존 알루미늄에 비해 3분의 2, 철의 5분의 1 수준의 무게로 최근 빠르게 수요가 늘고 있다.
대표적인 사례로는 르노삼성의 신형 SM7 Nova에 뒷좌석 파워시트와 트렁크의 맞닿는 부분에 포스코와 공동 개발한 마그네슘 판재를 최초 적용했다. 이는 세계 최초로 차량 차체에 마그네슘 판재를 적용한 것으로 기존 철강 소재 부품에 비해 무려 61%의 경량화에 성공했다.
이외에도 철강이 아닌 신소재를 이용한 방법도 각광 받고 있다. 탄소섬유강화플라스틱을 사용해 경량화 하면서도 강도는 철강에 비해 10배 이상 높일 수 있도록 하는 것이다. 무게는 현저히 줄어들면서도 인장력은 더욱 강력하다 보니 이미 고가의 고성능 차량들에는 널리 사용되고 있었지만 비싼 가격으로 널리 활용되지 못하고 있었다. 하지만 최근 적용범위가 점차 넓어지고 있다.
탄소유리섬유강화플라스틱소재가 본격적으로 투입된 차량은 얼마 전 새롭게 선보인 BMW의 플러그인하이브리드(PHEV) i8이다. 이차는 차량의 기본 외관부터 내부 곳곳에 이 소재를 적용해 무게를 획기적으로 줄이는 데 성공했다.
차량의 기본 무게를 줄이는 것도 중요하지만 휠의 무게를 줄이는 것도 연비향상에 많은 도움이 된다. 일반적으로 차량이 10% 가벼워지면 연비는 3.2%, 가속성은 8.5%, 조향성능은 19%가 향상된다. 하지만 휠의 경우 운동역학적인 측면에서 차량의 주행시 자체 중량보다 약 16배에 해당하는 차체중량을 받는다. 즉 휠 1개당 5Kg을 감량해 4개의 총 합20Kg을 감량하면 효과적으로 약 320Kg을 줄이는 효과를 볼수 있다.
이에 완성차 업체들이 기본 휠의 소재를 알루미늄으로 선택하는 것이다. 일부 소비자들의 경우 좀 더 가벼운 휠을 찾기 위해 마그네슘을 소재로 한 휠을 장착하는 경우도 있다.
이 밖의 방법으로 엔진의 다운사이징이 있다. 이는 몇 년 전 BMW가 활용해 성공적인 효과를 거둔 방법이다.
BMW는 기존 6기통이상의 고배기량차량들을 4기통으로 줄이고 여기에 터보차처를 활용해 출력을 향상시켰다. 이를 통해 BMW는 차량의 무게에 상당부분을 차지하는 엔진무게를 획기적으로 줄이는데 성공했다.
이를 통해 연비는 향상시키고 출력은 유지 할 수 있도록 했다. 기존 배기량과 출력이 비례한다는 인식을 불식시켰고 고출력을 유지하면서도 친환경성을 강조하며 두 마리 토끼를 모두 잡는데 성공했다.
업계관계자는 “완성차업체들의 이러한 노력을 뒷받침하기 위해 많은 부품사들도 노력을 아끼지 않고 있다”며 “앞으로도 더욱 향상된 연비를 위해 장기적으로 많은 연구개발이 필요할 것으로 예상된다”고 말했다.